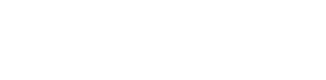
عیوب جوشکاری
دستیابی به اتصال جوشی رضایت بخش، احتیاج به روند سازمان یافته دارد که از طراحی اتصال و انتخاب روش جوشکاری شروع شده و با انجام عملیات جوشکاری و بازرسی آن پایان می یابد. طراح سازه باید از عوامل موثردر کیفیت جوشکاری مطلع بوده و آن ها را در طرح اتصالات خود به کار گیرد.
برای حصول جوش خوب باید پنج عامل زیر برآورده شود:
1) روش جوشکاری (Process selection)
2) آماده سازی درز (Preparation)
3) دستورالعمل جوشکاری (Procedure)
4) پرسنل (Personnel)
5) بازرسی و تایید جوش (Prove)
به مجموعه دستورالعمل های فوق، قانون پنج P گویند.در صورتی که روش ها و فنون صحیح جوشکاری رعایت نشود، ممکن است معایبی در سطح یا داخل فلز جوش به وجود آید. در اینجا به بررسی عیوب اصلی جوشکاری ، عوامل ایجاد و راههای جلوگیری از بوجود آمدن آنها می پردازیم.
ذوب ناقص (L.O.F) Lack of fusion)
عدم اتصال بین فلز جوش و فلز پایه یا بین پاسهای جوش .
عوامل ایجاد عیب :
1) عدم انتخاب صحیح اندازه و نوع الکترود مثلا استفاده از الکترودهای کوچک برای فولاد ضخیم و سرد
2) آمپراژ ناکافی و کافی نبودن انرژی ورودی: هنگامی که آمپراژ جوشکاری پایین باشد حرارت در قطعه کمتر می باشد و در نتیجه عمل ذوب به طور کامل انجام نمی شود از طرف دیگر هنگامی که آمپراژ در جوشکاری کم باشد الکترونهایی که از سمت الکترود به قطعه وارد می شود کمتر می باشد و در قطعه پایه عمل کندن توسط الکترون ها به طور کامل انجام نمی شوند و از این رو باعث به وجود آمدن عیب (ذوب ناکافی) می شود.
3) زاویه الکترود نامناسب: هر گاه زاویه الکترود ما به سمت قطعه ای تمایل بیشتری داشته باشد عمل ذوب در آن قطعه بیشتر انجام می شود و در قطعه دیگر ما برعکس به همین منظور در هنگام جوشکاری به زاویه الکترود باید توجه کامل شود تا عمل ذوب به طور مساوی بین دو قطعه مورد اتصال انجام شود.
4) سرعت حرکت بسیار زیاد : هنگامی که سرعت جوشکاری بالا باشد الکترودنهایی که از الکترود به فلز برخورد می کنند و موجب سوراخ کردن فلز می شوند کار خود را سریعتر انجام می دهندو ولی از سوی دیگر قطرات مذابی که می خواهند این کانال حفر شده را پر کنند نمی توانند وظیفه خود را به طور کامل انجام دهند و در حوضچه جوش در بعضی قسمتها مورد پوشش قطرات مذاب قرار نمی گیرند و در نتیجه آن قسمت ها خالی می ماند و باعث بوجود آمدن عیب عدم ذوب کافی می شود.
5) عدم تمیزکاری بین پاس ها و کثیف بودن سطح (پوسته نورد ، لکه ، روغن و …)
6) مناسب نبودن طرح اتصال
7) کافی نبودن گاز محافظ در فرآیندهای با پوشش گاز
8) انحراف قوس : هنگامی که قوس ما منحرف می شود تعادل قوس به هم می خورد و وقتی قوس به هر طرف منحرف شود طرف دیگر زیر بمباران الکترون قرار نمی گیرند و در نتیجه ذوب نمی شود به همین ترتیب ذوب در جوشکاری به طور کامل انجام نمی شود.
9) قطب الکترود : در زمانی که فقط به یک طرف قطعه دسترسی داریم باید قطبی را در جوشکاری انتخاب کنیم تا عمل ذوب ما کامل انجام شود. بیشترین نفوذ در جوشکاری در روش DC با قطب مستقیم می باشد (الکترود منفی دو قطعه کار مثبت)
نتیجه : اتصال جوش ضعیف میماند و به یک منطقه مستعد ایجاد خستگی تبدیل میشود.
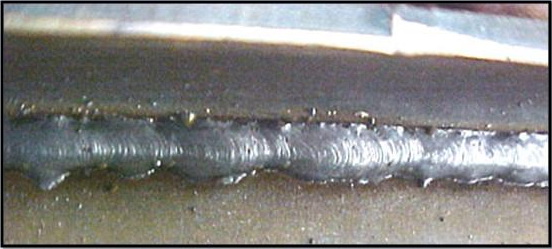
نفوذ ناقص( L.O.P) (Lack of pentertation)
عدم نفوذ کامل فلز جوش به ریشه اتصال
عوامل ایجاد عیب :
1) آمپر بسیار پائین
2) فاصله ریشه ناکافی
3) استفاده از الکترود با قطر بالا
4) سرعت حرکت زیاد
5) زاویه نامناسب دست
6) کثیفی درز
7) کم بودن زاویه پخ
نتیجه : ضعیف شدن اتصال و در نتیجه بوجود آمدن یک منطقه مستعد ایجاد خستگی و در نهایت باعث گسیختگی قطعه می شود.
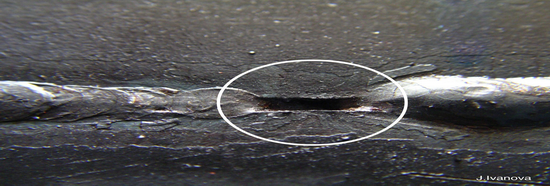
سوختگی یا بریدگی کناره جوش Undercut
شیاری در کنار یا لبه جوش که بر سطح جوش و یا فلز جوشی که قبلا راسب شده است قرار دارد. که به صورت منقطع یا پیوسته با عمق زیاد در سرتاسر مسیر جوش دیده می شود.
عوامل ایجاد عیب :
1) آمپر زیاد
2) طول قوس زیاد
3) حرکت موجی زیاد الکترود
4) سرعت بسیار زیاد حرکت جوشکاری
5) زاویه الکترود خیلی به سطح اتصال متمایل بوده است.
6) سرباره با ویسکوزیته زیاد
نتیجه : عوامل فوق موجب یک منطقه تمرکز تنش و یک منطقه مستعد برای ایجاد ترک خستگی میشود. که سرانجام منجر به شروع شکست یا خستگی یا تنشهای سیکلی می گردد.
برای جلوگیری از این عیب باید از حرکت زیگزاگی مناسب با مکث های کوتاه در کناره های لبه اتصال انجام داده و سرعت پیشرفت جوشکاری را کمی کاهش دهیم.
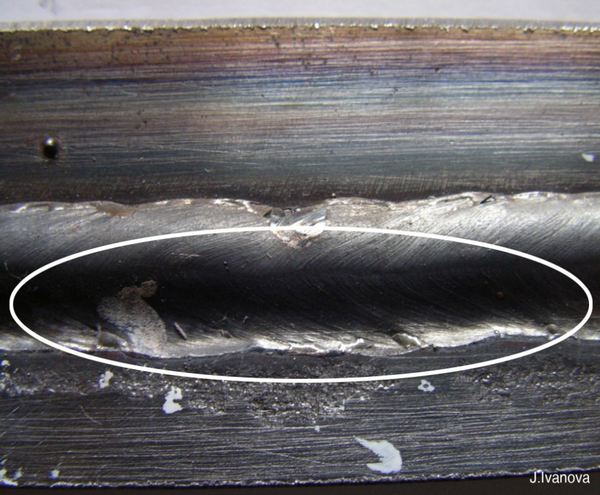
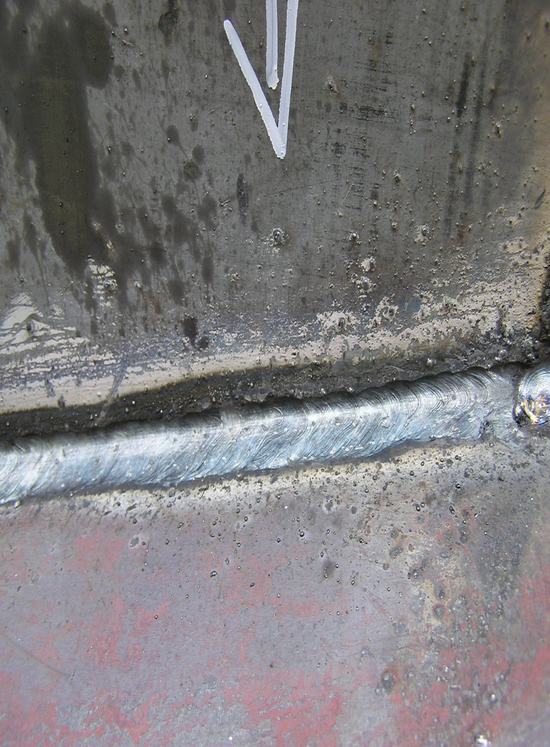
آخالهای سرباره Slag inclusion
به هر ماده غیر فلزی که در یک اتصال جوش بوجود میآید آخالهای سرباره میگویند؛ این آخالها میتوانند در رسوب جوش نقاط ضعیفی ایجاد کنند. منبع این ذرات لزوما از پوشش الکترود یا سرباره نیست بلکه محصول واکنش های مختلف سرباره ، گاز و فلز نیز می تواند باشد.
عوامل ایجاد عیب :
1) پاک نشدن مناسب سرباره از پاسهای قبلی
2) آمپراژ ناکافی
3) زاویه یا اندازه الکترود نادرست
4) آماده سازی غلط
5) ریخته شدن پوسته شکسته شده الکترود به درون مذاب
6) ورود هوا در اثر سهل انگاری جوشکار در حرکات نامناسب الکترود و یا مشعل
نتیجه : آخالهای سرباره استحکام سطح مقطع جوش را کاهش میدهند و یک منطقه مستعد ترک ایجاد میکنند. مقدار کم این ذرات تاثیر چندانی بر روی خواص مکانیکی ندارد اما مقدار زیاد و بویژه ابعاد بزرگ و طویل بر روی خواص مکانیکی بویژه مقاومت ضربه ای فلز جوش تاثیر منفی می گذارد.
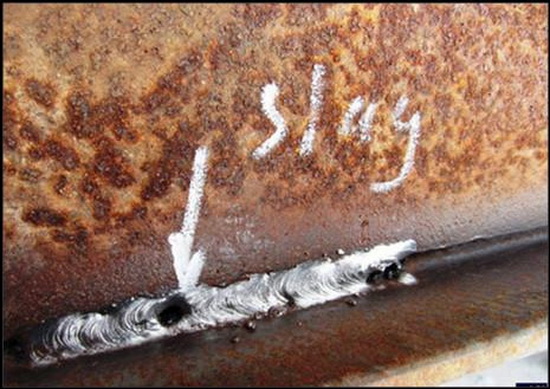
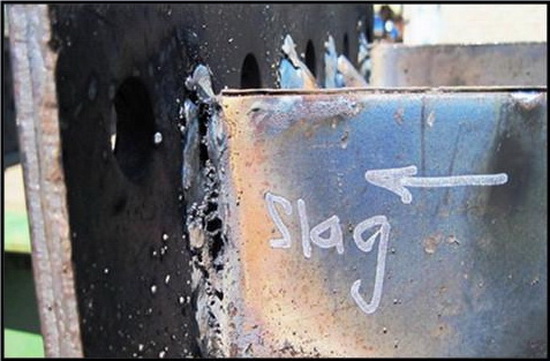
روی هم افتادگی (انباشتگی جوش در کنارهها) over lap or over roll :
نقصی در کنار یا ریشه جوش که به علت جاری شدن فلز بر ری سطح فلز پایه ایجاد می شود بدون اینکه ذوب و جوش خوردن با آن ایجاد شود. این عیب در جوشکاری با الکترود دستی و در وضعیت قائم بیشتر اتفاق می افتد که معمولا در اثر زاویه اشتباه الکترود یا قطعه کار می باشد.
عوامل ایجاد عیب :
1) سرعت حرکت کمتر از حالت نرمال یا طبیعی
2) زاویه نادرست الکترود
3) استفاده از الکترود با قطر بالا
4) آمپراژ خیلی کم
نتیجه : عوامل فوق کاری مانند بریدگی کناره جوش دارد و یک منطقه تمرکز تنش از فلز جوش ترکیب نشده ایجاد میکند.
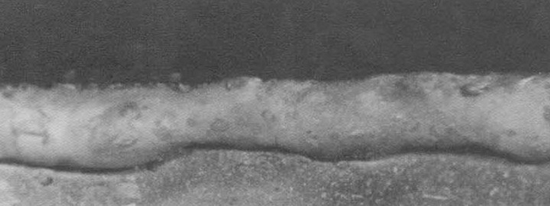
تخلخل Porosity
تخلخل سوارخ یا حفرهای است که به صورت داخلی یا خارجی در جوش دیده میشود. تخلخل میتواند از الکترود مرطوب ، الکترود روکش شکسته یا از ناخالصی روی فلز پایه ایجاد شود. همچنین تخلخل بصورت مک لولهای ، مک سطحی و سوراخهای کرمی نیز دیده میشود.
عوامل ایجاد عیب :
1) سطح فلز پایه آلوده مثل آلودگیهای روغن ، غبار ، لکه یا زنگار
2) مرطوب بودن روکش الکترود
3) محافظت گازی ناکافی قوس
4) فلزات پایه با مقادیر بالای گوگرد و فسفر
5) زمان ناکافی برای فعل و انفعالات متالورژیکی در حوضچه جوش
نتیجه : به شدت استحکام اتصال جوش شده را کاهش میدهد. تخلخل سطحی به اتمسفر خورنده اجازه میدهد که فلز جوش را مورد حمله قرار دهد و موجب نقص در آن شود.
1.خلل و فرجی که در چند سانتی متری اولیه شروع جوشکاری با استفاده بعضی از الکترودها مشاهده می شود: این عیب در اثر فقدان اکسیژن زدایی کافی در ابتدای جوش است در پوشش الکترود ها معمولا مقداری مواد اکسیژن زدا نظیر فرو سیلیسیم وجود دارد. در فولادهای آلیاژی با استحکام بالا درصد سیلیسیم در جوش معمولا از میزان معینی نباید بیشتر شود (حدود 35/0%) چون اثر معکوس بر روی درجه حرارت انتقال نرمی به تردی (Transition temperature) در استحکام ضربه ای می گذارد بدین جهت در الکترودهای مصرفی در اینچنین فولادها نظیر سری های E100 و E110 و. E120 از نظر حضور فروسیلیسیم و گاه بعضی از عناصر اکسیژن زدایی دیگر محدودیتی وجود دارد. اما با پیشرفت عملیات جوشکاری و حضور بیشتر و فعال تر سرباره حاصل از پوشش الکترود طبیعتا حضور اتمسفر هوا در منطقه حوضچه جوش کاهش یافته و این عیب به وقوع نمی پیوندد. در اینمورد برای پرهیز از وقوع این نوع خلل و فرج تدابیر مختلفی پیش بینی شده است که در مورد آنها مختصرا در زیر توضیح داده می شود.
الف:شروع عملیات جوشکاری بر روی قراضه فولادی که قبلا در ابتدای مسیر عملیات جوش الصاق شده است انجام شود و پس از خاتمه جوش از قطعه کار جدا می شود واضح است که این تدبیر در بعضی موارد ممکن است اقتصادی نباشد.
ب:تکنیک یک گام عقب Back-step: نقطه شروع کمی عقب تر از محل شروع واقعی است پس از آغاز جوشکاری الکترود به ابتدای مسیر اتصال هدایت شده و عملیات جوشکاری ادامه می یابد. بدین ترتیب اگر خلل و فرج نیز ایجاد شده باشد با برگشت قوس و ذوب مجدد آن به احتمال زیاد بر طرف می شود.
2.خلل و فرج در دامنه انجماد : این نوع حفره ها ممکن است در سرتاسر جوش مشاهده شود و خود دارای دو نوع شکل است خلل و فرج های کروی شکل که به صورت متمرکز یا پراکنده در زیر جوش یا حتی روی جوش دیده می شود. نوع دیگر که به سوراخ های «کرمی» شکل Worm-holes یا مک هوا Blow holes مرسوم است.
بعضی گازها در مذاب دارای حلالیت بوده که در درجه حرارتهای بالا مقدار این حلالیت افزایش می یابد. نمونه ای از این چنین گازها هیدروژن می باشد که حاصل تجزیه رطوبت وارد شده به مذاب فلز جوش است. در ضمن سرد شدن مذاب پس از اینکه حجم هیدروژن در مذاب از حد اشباع گذشت، مقدار اضافی بصورت حبابهایی شروع به جوانه زدن، رشد، شناور شدن و در صورت امکان خارج شدن از مذاب می نماید. احتمال واکنش هیدروژن اضافه بر حد اشباع با C,O و S و تولید گازهای ملکولی دیگر نظیر H2O، SO2 و CH4 و … نیز وجود دارد که در این حال محصول واکنش بصورت حبابهایی از مذاب بیرون رفته و یا محبوس می گردد.
ازت جذب شده از هوا نیز تا حدودی رفتاری مشابه داشته و می تواند عامل تخلخل باشد. علاوه بر آن ازت می تواند تولید ترکیب های تیرید کند که اغلب تاثیر سو بر روی خواص مکانیکی جوش دارد.
عامل دیگر حبابهای گاز CO می باشد. در فلز جوش فولادهای کربنی (بویژه با کربن بالا) معمولا اکسیژن حل شده ممکن است وجود داشته باشد. در دامنه انجماد، مذاب، محصور در جامد به دلیل جدایش از کربن غنی شده و احتمال واکنش زیر بیشتر می شود.
C+O= CO
در مواردی که مواد اکسیژن زدا نظیر Si Mn و غیره به اندازه کافی وجود نداشته باشد. واکنش فوق تسریع می شود واکنشی مشابه در مورد گوگرد نیز می تواند اتفاق افتد که حاصل آن حبابهای گاز SO2 و یا SH2 می باشد. بعضی ترکیبات فرار آلی یا غیرآلی موجود در مواد معدنی پوشش الکترود و پودر جوش و یا آلودگی ها (نظیر چربی، رنگ و غیره) در روی سطح مسیر اتصال همچنین تجزیه ترکیباتی نظیر کربنات ها در ترکیب مواد در درجه حرارت بالا، عوامل دیگر در ایجاد گاز در حوضچه جوش و بالاخره خلل و فرج می باشند.
با توجه به نکات بالا و نحوه توزیع حرارت در حوضچه جوش (درجه حرارت بالا در زیر قوس یا شعله و درجه حرارت پایین با شیب زیاد در انتها و دیواره حوضچه جوش) و رشد کریستالهای ستونی جامد از دیواره ها بطرف وسط و سطح حوضجه جوش، می توان پیش بینی کرد که در سطح انجماد گازها به حالت اشباع در آمده و مقدار اضافی از این حد به صورت حبابهائی در روی دانه های جامد جوانه زده و رشد می کنند. در صورت شرایط مناسب فاصله انجماد زیاد و ویسکوزیته پایین مذاب و زمان کافی حبابها می توانند به سطح مذاب آمده و خارج شوند. در مواردیکه شرایط مناسب نباشد حبابها به حالت شناور یا در حین تکامل در لابلای دانه های جامد در حال رشد حبس شده و به صورت خلل و فرج یا سوراخهای کرمی شکل در فلز جوش باقی می مانند. همانطور که مشاهده می شود حباب گاز در بین ستونهای کریستالهای جامد چندین دفعه تلاش می کند تا بصورت کروی جدا و به سطح مذاب شناور شود که ادامه رشد کریستالهای جامد دیگر آنرا محبوس کرده و در آخر شکلی شبیه کرم بخود می گیرد. این سوراخها ممکن است به طور چندین میلیمتر و حتی تا سطح جوش نیز ادامه یابد.
نوع دیگر از خلل و فرج در حین ذوب و انجماد ناشی از سهل انگاری جوشکار در مصرف الکترودهایی است که قسمتی از پوشش آن شکسته و جدا شده است و یا برای صرفه جویی از قسمت انتهایی الکترود که بدون پوشش است نیز استفاده کرده است.
برای کاهش خلل و فرج حین انجماد نباید تصور کرد که اگر درجه حرارت مذاب به کمک پارامترهای جوشکاری بالا برده شوند ویسکوزیته کمتر شده و حبابها بهتر رها می شوند زیرا افزایش درجه حرارت میزان حلالیت گازها را درمذاب نیز بیشتر می کند. بنابراین تنها راه جلوگیری از ورود گازها یا حذف عوامل ایجاد گاز نظیر رطوبت ، چربی و … است.
به عنوان مثال با پیش گرم کردن الکترود و یا انتخاب نوع مناسب میزان هیدروژن ورودی را با کاهش طول قوس احتمال ورود اکسیژن و ازت، با انتخاب نوع مرغوب تر فولاد (با گوگرد کمتر) شانس ایجاد SO2 و SH2 و همچنین با انتخاب الکترود با مواد اکسیژن زدایی بیشتر (در پوشش) امکان ایجاد CO2 را می توان کاهش داد.
در فرآیندهایی که از گاز محافظ استفاده می شوند تدابیر کمی فرق می کند. ترکیب فشار و دبی گاز محافظ، قطر نازل، فاصله نازل تا سطح کار و پارامترهای دیگر نیز باید مورد دقت و توجه قرار گیرد.
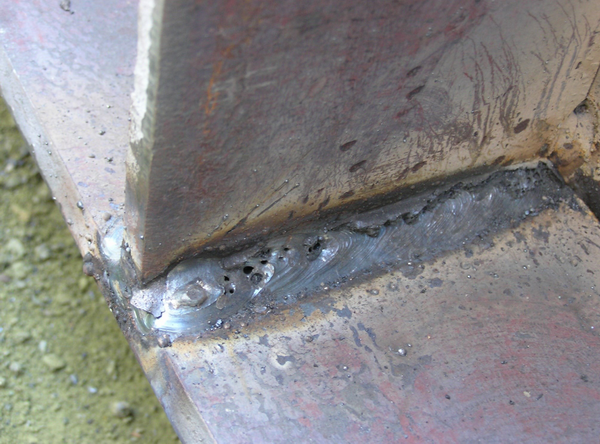
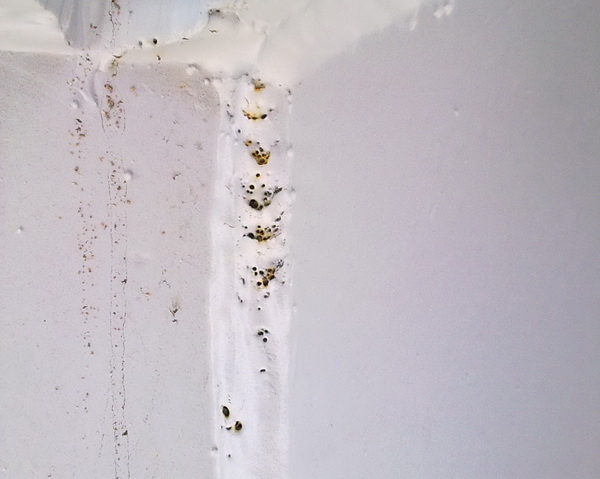
همراستا نبودن اتصال جوش Join misagnment
این مشکل معمولا همراستا و همسطح نبودن قطعاتی که به هم جوش میشوند نامیده میشوند. عدم همراستایی یک مشکل معمول در آماده سازی روشهای لب به لب است و هنگامی ایجاد میشود که صفحات ریشه و صفحات اتصال از فلز پایه در محل درست خود برای جوشکاری قرار نگرفتهاند.
عوامل ایجاد عیب :
1) مونتاژ نادرست قطعاتی که باید جوش شوند.
2) خال جوشهای ناکافی که میشکند یا بست زدن ناکافی که موجب حرکت میشود.
نتیجه : همراستا بودن جدی است، زیرا نقص در ذوب لبه ریشه موجب ایجاد مناطق تمرکز تنش میشود در سرویس دهی موجب شکست خستگی زود رس اتصال میشود.
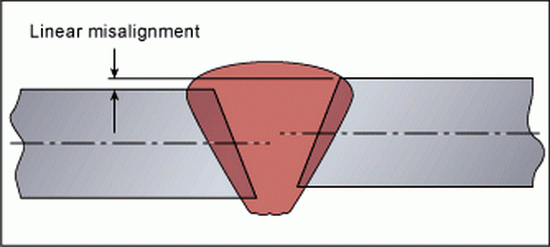
ترک جوش Weld cracking
ترک برداشتن یکی از مهمترین و مضرترین عیب در جوشکاری می باشد. از یک طرف احتمال وقوع آن در ردیف گسترده ای از فولادها و فلزات و آلیاژهای غیرآهنی وجود دارد. از طرف دیگر موضوع پیچیده است چون اولا شکل ها ، ابعاد، جهت ها و اندازه های مختلف داشته. ثانیا در محل های مختلف از فلز جوش Weld metal، خط ذوب Fusion line و منطقه مجاور جوش Heat affected zone (HAZ) ایجاد می گردد. از این مهمتر دلایل گوناگونی از قبیل ترکیب شیمیائی مواد مصرفی (فلز قطعه کار، مفتول یا الکترود پودر یا فلاکس و گاز محافظ) پارامترهای جوشکاری (آمپر، ولتاژ، سرعت، قطب) طراحی قطعه و محل اتصال و شرایط عملی و تکنیکی در جوشکاری می توانند سبب تشدید یا تقلیل نوع خاصی از ترک برداشتن شود. بطور شماتیک انواع گوناگون ترکیدگی را در مناطق مختلف نشان می دهد که برحسب محل و امتداد به نام های خاصی شناخته شده اند و عبارتند از:
1) ترکیدگی در حوضچه جوش یا دهانه انتهایی Weld metal crater cracking
2) ترک عرضی در جوش Weld metal Transwerse cracking
3) ترک عرضی در منطقه مجاور جوش H.A.Z Transwerse cracking
4) ترک طولی در فلز جوش Weld metal longitudinal cracking
5) ترکیدگی زبانه یا گوشه ای Toe cracking
6) ترکیدگی زیر فلز جوش under bead cracking
7) ترکیدگی در خط ذوب Fusion line cracking
8) ترک ریشه فلز جوش Weld metal root cracking
یکی از عوارض مهم ترک غالبا شکسته شدن قطعه بدون تغییر فرم پلاستیکی است که اصطلاحا شکست ترد Brittle fracture می نامند. این نوع شکست در اثر پیشرفت کند ابتدایی ترک برداشتن و پس از ادامه آن تا حد معینی (حد بحرانی طول ترک) پیشرفت بسیار سریع است و ترک برداشتن در زمان کوتاه بدون نیاز به تنش ادامه یافته و شکست بوقوع می پیوندد. بالانتیجه در این مرحله فرصت برای جلوگیری از شکستگی و گسیختگی کامل اتصال کم است و گاه سرعت پیشرفت ترک برداشتن به چندین متر در ثانیه می رسد.و منجر به حوادث تلخ با خسارات مالی و جانی فراوان می شود نظیر دو نیم شدن کشتی در دریا.
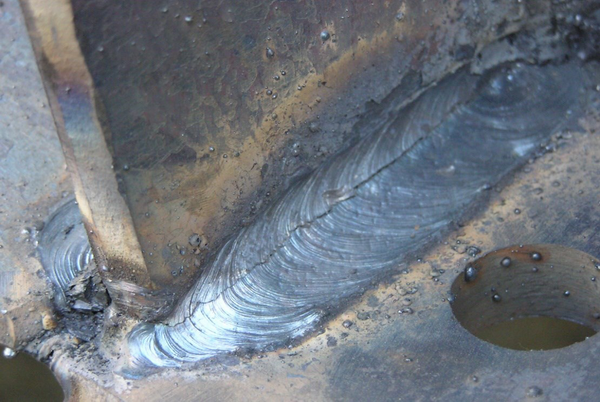
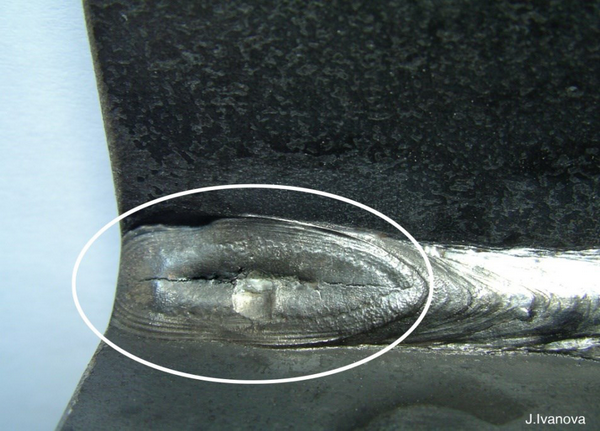
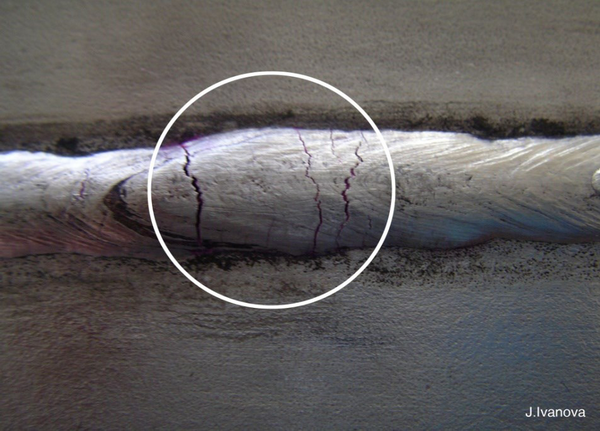
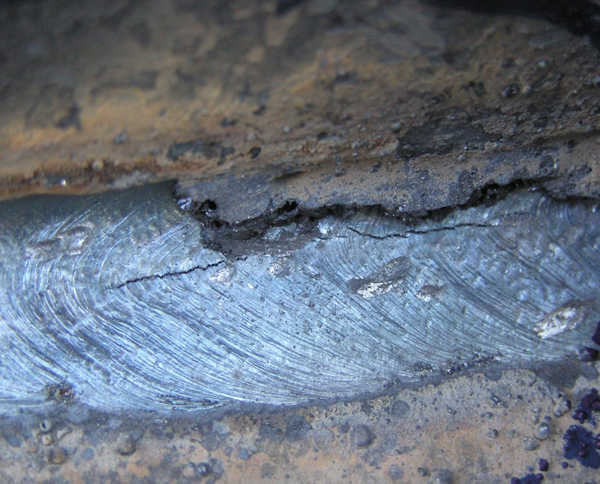
1.ترک گرم یا فوق خط انجماد: دو شرط یا حالت لازم است تا در دامنه انجماد در جوش ترکیدگی ایجاد شود. اولا باید نرمی و انعطاف پذیری ductility فلز به اندازه کافی نباشد ثانیا تنش کششی ایجاد شده بین کریستالهای جامد ناشی از انقباض از تنش شکست Fracture stress فلز در آن درجه حرارت تجاوز کند. در هنگام سرد شدن کریستالهای جامد جوانه زده و رشد می کنند غلظت بعضی عناصر و ناخالصی ها در فاز مایع باقیمانده افزایش می یابد. از درجه حرارت معینی به بعد اتصال کریستالهای جامد بصورت نوعی چسبیدگی می باشد که استحکام در بین کریستالها ظاهر می شود اما نرمی و انعطاف پذیری صفر است. در ادامه سرد شدن از درجه حرارت خاص دیگر nil-dutility temperature خاصیت انعطاف پذیری نیز مشهود می گردد که با شیب زیادی همراه با سرد شدن جامد افزایش می یابد. این افزایش پس از یک ماگزیمم دوباره رو به کاهش می گذارد فاصله درجه حرارت تردی می نامند که یک عامل مهم و مشخص کننده حساسیت فلز در مقابل ترک برداشتن می باشد.
تردی در منطقه انجماد در اثر حضور لایه های مایع بین دانه های ناپیوسته جامد است. این فاز می تواند یک فاز یوتکتیک و یا حاصل تجمع ناخالصی ها باشد. وقتی این لایه بوجود می اید که مایع خاصیت خیس کردن Wetting بر روی دانه ها را داشته باشد یا با بیان دیگر انرژی سطحی Surtace energy نسبت به مرز دانه ها پایین باشد. بنابراین سولفور منگنز که تمایل به کروی شدن دارد کمک به کاهش حساسیت فلز در برابر این نوع ترک برداشتن می کند . تنش حاصل از انقباض در حین سرد شدن برابر است با که E مدول یانگ، ضریب انبساط حرارتی، x فاکتور ممانعت یا مهار restraint و تغییر درجه حرارت است. احتمال اینکه این تنش در فاصله نسبتا بزرگ از استحکام کششی تجاوز کند زیاد است و چون نرمی نیز وجود ندارد ترک برداشتن یا شکست اتفاق می افتد.
به فاکتور x نیز باید توجه شود که به مقدار زیادی به طرح اتصال ناموزنی اسکلت مورد جوش، مقدار فاصله بین لبه های ورق مورد جوش، ضخامت ورق و نسبت ضخامت ورق به مقطعه جوش بستگی دارد.
ترک برداشتن در دهانه انتهایی فلز جوش یکی از انواع ترکیدگی گرم می باشد. دهانه انتهایی چون سریعتر از قسمتهای دیگر فلز جوش سرد می شود. همچنین انجماد از تمام اطراف شروع و ادامه می یابد. احتمال وقوع حفره های انقباضی و ترک های ناشی از آن Shrinkage crack افزایش می یابد. برای کاهش یا جلوگیری از این عیب بهتر است از ایجاد حوضچه یا دهانه انتهایی در خاتمه مسیر جوش جلوگیری کرد. بابالا بردن و افزایش فاصله الکترود نسبت به سطح کار افزایش سرعت و یا کاهش تدریجی شدت جریان و یا افزایش غذا دادن مفتول (فرآیند جوشکاری TIG یا اکسی استیلن) می توان حتی المقدور این دهانه را بصورت مسطح و یا کم عمق تر درآورد.
ترک برداشتن خط ذوب یا نفوذ و حتی ترکیدگی در منطقه مجاور جوش نیز ممکن است از نوع ترک گرم باشد. بعضی آلیاژها دارای عناصر یا ناخالصی هایی هستند که تولید فازی در مرز دانه ها می کنند که این فاز یا دارای نقطه ذوب پایین بوده و یا باعث می شود که استحکام بین دانه ها را در درجه حرارت نسبتا بالا کاهش دهد سولفیدها کاربیدها با ترکیب پیچیده و یا ترکیبات بین فلزی Intermetallic copound از این مواد محسوب می شوند. حال اگر این آلیاژها تحت سیکل حرارتی جوشکاری قرار گیرند نقاطی بسیار نزدیک به منطقه ذوب درجه حرارت حدود 1300-1150 درجه سانتیگراد می باشد لایه بین دانه ها ذوب شده و با در این درجه حرارت استحکام و فرم پذیری پایین تحت تنش های ناشی از انقباض فلز جوش قرار گرفته و در نتیجه ترکیدگی گرم بوجود می آید.
در اثر نفوذ هوا و اکسیده شدن سطح ترک در درجه حرارت نسبتا بالا غالبا مقطع ظاهری شکست در ترکیدگی های گرم قهوه ای می باشد (در مورد فولادها) گاه با مشاهده این رنگ می توان حدود درجه حرارت شکست را حدس زد.
ترک گرم می تواند در اثر ذرات سرباره محبوس شده (آخال) نیز حاصل شود. اغلب الکترودها و یا فلاکس ها حاوی موادی در ترکیب خود می باشند تا بتواند سرباره ای با وزن مخصوص و نقطه ذوب پائین ایجاد نماید . بدین ترتیب احتمال حبس شدن ذرات سرباره در فلز جوش کم شود.
ترکیدگی در امتداد طولی از قطعه کار در نزدکی یموضع اتصال نیز مشاهده شده است. که ناشی از وجود ذرات طویل شده سرباره در فلز قطعه کار است که این ذرات در ضمن تهیه و نورد فولاد بوجود آمده اند. این نوع ترکیدگی به پارگی سراسری Lamellar tearing مرسوم است.
2.ترک سرد یا زیر خط انجماد : هنگامی که ترک در عرض دانه ها ادامه می یابد و علائمی دال بر تمایل پیشرفت ترک در مرز دانه ها مشاهده نشود. به احتمال زیاد ترک از نوع سرد یا زیر خط انجماد است. همانطور که اشاره شد ترک گرم معمولا بالای 1200 درجه فارنهایت (650 درجه سانتیگراد) در حین جوشکاری یا سرد شدن ایجاد می شود. در ادامه سرد شدن تا 600 درجه فارنهایت (316 درجه سانتیگراد) غالبا ترکهایی ایجاد گردد. اما از این درجه حرارت به پایین ممکن است بعد از یک ساعت چند روز چندین هفته پس از جوشکاری ترکهایی ایجاد و رشد یابند که آنها را ترک های سرد می نامند.
شرایط مورد نیاز برای ایجاد ترکهای سرد نیز تقریبا مانند ترک های گرم توام شدن تردی در فلز جوش یا منطقه مجاور آن و تجاوز تنش کششی ناشی از انفصال (یا عوامل دیگر) از حد تنش شکست تردی در این مرحله ممکن است به دلایل بوجود آید از جمله در بعضی آلیاژها فازهایی وجود دارد که در ضمن حرارت (ناشی از جوشکاری)ذوب شده و پس از انجماد و سرد شدن تولید مناطق موضعی و شکننده کنند. دربرخی دیگر تغییر فاز در اثر سیکل حرارتی ناشی از عملیات جوش باعث ایجاد مناطق ترد و شکننده می شود که ایجاد مارتنزیت در بعضی فولادهای یا پرکردن از این نمونه است.
به علت تداخل عوامل متعددی از قبیل جنس مواد مصرفی فرآیند جوشکاری شیب حرارتی، توزیع تنش، نرخ بارگذاری، محیط خورنده و غیره. تشخیص دقیق و یا علل واقعی ایجاد ترک بسیار مشکل است. غالبا ترک سرد در اثر یک عامل حاصل از انجماد نیز می تواند بعدا در اثر عوامل تشدید کننده در درجات پائین و ترک سرد حاصل نمایند. بطور کلی حالتهایی که احتمال ایجاد ترک سرد را افزایش می دهند عبارتند از:
1) ترد و سخت شدن منطقه مجاور جوش
2) ایجاد و پیشرفت تنش های واکنشی و پسماند
3) هیدروژن تردی
ساختار میکروسکپی فولاد قطعه کار یکی از فاکتورهای مهم در ترک سرد است.
گاه تنش ایجاد شده به حدی نیست که موجب ترکیدگی شود اما بصورت تنش پسماند در قطعه مانده و در حین کاربرد قطعه تحت شرایط خاص اعمال نیرو و تنش وارده مجموع آنها از حد تنش پارگی تجاوز کرده و ترک سرد و گسیختگی زود هنگام شروع می شود. بنابراین عملیات حرارتی با پس گرم کردن ممکن است در بعضی موارد باعث جلوگیری از ایجاد ترکیدگی سرد شود. پیش گرم کردن برای تقلیل سرعت سرد شدن و جلوگیری از ایجاد فاز ترد تدبیر مفید دیگری است.
همانطور که قبلا اشاره شد علاوه بر ساختار میکروسکپی نامناسب تاثیر تنشهای واکنش و باقیمانده هم حائز اهمیت است ترکیدگی ممکن است توسط تنشهای واکنشی ایجاد شود که قابلیت تغییر فرم پذیری ندارند. غالبا در ورقهای نازک تنش ها دو محوری و در ورقهای ضخیم سه محوری می باشند. یکی از عوامل که تشدید کننده تنشها در محل اتصالات است شکاف یا درز می باشد تنش ایجاد شده در ریشه شکاف با ازدیاد عمق شکاف افزایش می یابد.
نفوذ ناقص ریشه جوش در اتصال یکطرفه لب به لب با سر به سر نیز عامل تشدید کننده ترک ریشه ای root cracking است.
ارتفاع زیاد گرده جوش بالنتیجه زاویه کوچک گوشه جوش Reentrant angle و زیر-برش یا سوختگی کناره جوش Under cut می توانند تشدید کننده و تمرکز دهنده تنش در موضع خاص و کوچکی شوند که احتمالا نتیجه آن ترک گوشه ای خواهد بود.
عامل سوم و موثر بر روی ترک سرد مقدار هیدروژن در جوش است (غالبا از طریق رطوبت و چربی ها وارد مذاب می شود) تئوری و مکانیسم هیدروژن تردی بسیار مفصل و پیچیده است که بطور خلاصه بررسی می شود.
بعلت کوچکی اندازه اتمها ی هیدروژن این عنصر در فولاد می تواند به راحتی حل شده و در حالت جامد هم به شبکه اتمی آهن نفوذ نموده و از جایی به جایی دیگر حرکت کند. تاثیر قوی تردی هیدروژنی بر روی ایجاد ترکیدگی سرد موضع جدیدی نیست که در سیم و ساختن فنرها تاثیر هیدروژن بر روی ترد شدن آنها مطالعه شده است.
حال اگر فلز جوش که با الکترود دستی بر روی فولاد رسوب داده شده در نظر گرفته شود ممکن است حدود gr100/ml30 (میلی لیتر درصد گرم فلز جوش) هیدروژن در مذاب فلز جوش حل شده باشد که همزمان با سرد شدن مذاب حلالیت گاز کم شده و مقداری از هیدروژن بصورت ملکول گازهای دیگر به خارج رها می شوند. ولی بعلت سرد شدن مذاب فلز جوش مقداری از گاز هیدروژن در جوش محبوس می شود که در ادامه سرد شدن به حد اشباع می رسد. مقداری از اتمهای هیدروژن به اطراف نفوذ کرده و حتی به سطح فلز آمده و آزاد می شوند. مقدار دیگر از آن به ساختار کریستالی یا شبکه اتصال فولاد که درآن هیدروژن حل شده کمتری است و یا به هر فضای آزاددیگر شامل حفر ناپیوسته ساختار کریستالی discontinuities در داخل فلز منتقل می شوند. واضح است که این نرخ نفوذ نیز با پائین آمدن درجه حرارت کاهش می یابد.
با توجه به نکات بالا می توان گفت که میزان هیدروژن باقیمانده در فلز جوش به میزان تاثیر هیدروژن به مشخصات زیر بستگی دارد:
1) واکنش با اکسیژن، کربن، کوگرد و احیانا عناصر دیگر و ایجاد ترکیب گازی
2) نفوذ در حفره ها و ملکولی یا حباب شدن آنها
3) داخل شدن به فضای خالی اطراف ذرات ناخالصی ها و احتمالا بصورت آب در آمدن (احیانا اکسید)
4) جذب شدن به منطقه مجاور جوش
5) نفوذ کردن به سطح و آزاد شدن در هوا
واضح است درجه حرارت بین پاسی Inter pass temperature و زمان نگهداری جوش در درجه حرارت محیط یا احتمالا درجه حرارتی بالا می تواند بر مبنای هیدروژن باقیمانده و موارد فوق تاثیر بگذارد.
در مورد مکانیسم هیدروژن تردی تئوریهای مختلفی موجود است. نخستین تئوری می گوید هیدروژن اتمی حل شده فوق اشباع در شبکه کریستال می تواند در روی سطح گونه حفره های کوچک و یا درزهای ریز بین ناخالصی ها در مرز دانه ها Perfection یا درزهای ریز در اطراف ذرات ناخالصی ها rifts and voids رسوب یا حل شود Precipitate. در این مواضع بسیارکوچک هیدروژن از حالت اتمی بصورت مولکولی در میآید و بعلت رابطه مجذوری که بین فشار مولکلولی با فشار اتمی هیدروژن جذب شده وجود دارد. فشار زیادی در این حفره ها و درزهای کوچک ایجاد می گردد. بعنوان مثال مقدار 1ml/100gr هیدروژن جذب شده می تواند فشاری در حدود Psi200000 تولید کند. عقیده بر این است که این فشار میتواند تنش های سه بعدی لازم برای ایجاد منبع حساس در برابر شکست را بوجود اورد.
تئوری دیگر معتقد است که رسوب و جدایش هیدروژن در سطوح عیوب کریستالی Internal lattice imperfection rifts باعث کاهش انرژی سطحی و پائین آوردن تنش می شود که می تواند سبب وسعت دادن درزهای فوق میکروسکوپی Submicroscopic rifts به ترکیدگی شود هر دو تئوری براساس تنش های حاصله از دیفوزیون و رسوب هیدروژن مطرح شده است.
عقیده کلی برآنست که تردی هیدروژنی و ترک ناشی از آن در سه مرحله :
1) تامل Incubation
2) رشد آهسته ترک
3) رشد ترک با سرعت بالا حتی به مناطقی که هیدروژن کمی هم دارند.
حاصل می شود.
هیدروژن تمایل دارد در نواحی تنش های سه محوری که استحکام چسبندگی Cohesive strength کم است متمرکز شود. بعنوان مثال در نواحی اطراف عیوب ترکهایی مویی یا شکاف سطحی هنگامیکه غلظت تمرکز و تجمع هیدروژن در این نواحی پرتنش به حد معینی رسید نطقه ترک ایجاد شده و رشد آن در محل هایی که استحکام شکست بالاتری دارند احیانا متوقف می شود اما به محض توقف ترکیدگی دوباره منطقه تنش سه بعدی و متمرکز شدن هیدروژن شروع شده و احتمالا این سیکل تکرار می شود تا به حد بحرانی طول ترک برسد.
درجه تردی تولید شده توسط هیدروژن مقداری به استحکام فولاد بستگی دارد به طور کلی تردی به ازا مقدار معینی از هیدروژن با افزایش استحکام فولاد ازدیاد می یابد بعنوان مثال فولادهای خیلی مقاوم (استحکام حدود Ksi300) می تواند حتی با مقدار 1ml/100gr هیدروژن ترد و شکننده شود و این اثر مشهود گردد.
همانطور که اشاره شد یکی از فاکتورها نفوذ و تحرک هیدروژن از ناحیه ای به ناحیه دیگر است و این فاکتور خود متاثر از درجه حرارت است . عملا بین F 200-150 درجه تا بیشترین اثر تردی هیدروژنی مشاهده شده است. در درجه حرارت های بالا مقدار دیفوزیون به حدی است که هیدروژن می تواند از سطح فلز بخارج رها شود.
نرخ اعمال تنش و همچنین ضخامت قطعه فاکتورهای دیگری هستند که خالی از اهمیت نیستند. در بررسی ایجاد ترکهای سرد در جوشکاری این نکته را نباید فراموش کرد که در یک حد تنش ماکزیمم است که ترک برداشتن هیدروژنی بدون وقفه پس از سرد شدن جوش از حدود 200 درجه فارنهایت ایجاد می گردد و در یک حد مینیمم تنش این نوع ترکیدگی در حالت استاتیکی ایجاد نمی گردد. در بین این دو حد تنش این پدیده احتمالا با تاخیر بوقوع می پیوندد.
یک نمونه از ترک سرد ناشی از هیدروژن غالبا در زیر فلز جوش در منطقه ای بسیار نزدیک آن بنام ترکهای ریز فلز جوش Underbead creaking در فولادهای آلیاژی دیده می شود که بسته به وضعیت توزیع تنش های پسماند ، موقعیت تشدید کننده تنش Stress raiser و یا نیروهای اعمال شده در امتداد و جهت های متفاوت حتی از منطقه مجاور جوش بطرف فلز قطعه کار در فاصله ای دورتر هم پیشرفت کرده و مشاهده می شود.
اما بهر حال هیدروژن می تواند فلز جوش را نیز ترد کرده و نوعی از ترک سرد را بوجود آورد. این عیب بنام چشمهای ماهی Fisheyes از زمان نسبتا طولانی شناخته شده است. چشم ماهی معمولا توسط یک نوع ناپیوستگی شبیه حفره های گاز gas pocket با ذرات محبوس شده غیر فلزی احاطه شده است.
ظاهرا هنگامیکه اتم هیدروژن در سطح حفره ها یا ترکهای ریز رسوب کرده و به فرم مولکولی در می آید فشار حاصل می تواند به اندازه کافی بزرگ باشد تا سبب یک تغییر طولی یا کش آمدن در کریستالهای شبکه اطراف حفره می باشد. این حوزه تنش ممکن است به اندازه ای که در شکاف تیز یا ترک ایجاد شده و منجر به ادامه ترک برداشتن می شود شدید نباشد ولی این حوزه تنش موضعی می تواند سبب نفوذ بیشتر هیدروژن به این منطقه شود. هنگامی که فلز جوش تحت نیرو یا کش آمدن با نرخ نسبتا آرام (تحت کشش یا خمش) قرار گیرد هیدروژن بیشتری به محیط اطراف حفره نفوذ کرده و این سطوح و مناطق موضعی به صورت مسطح با شکست ترد گسسته می شود. بعلت زمان کم ادامه مکانیسم تردی هیدروژن در کلیه مناطق امکان پذیر نخواهد بود و بقیه مناطق همراه با مقداری تغییر فرم پاره می شود و ظاهر سطح مقطع شکست به شکلی دیگر مشهود می شود.
برای کاهش ایجاد چشمهای ماهی کافی است که قطعه را قبل از آزمایش در در جه حرارتی بین 1300-200 درجه فارنهایت (700-900درجه سانتیگراد) برای مدت زمان معین حرارت داد. طبیعتا در جه حرارت پائین کمتر با ضخامت زیادتر به زمان بیشتری نیاز دارد. بدین ترتیب مقداری از هیدروژن تحت قوانین نفوذ خارج می شود. مقطع شکسته شده نمونه آزمایش ضربه تعداد کمتری چشمهای ماهی را نشان می دهد و این نتیجه تائیدی مکانیسم گفته شده در بالا است.
بطور کلی سه تدبیر اساسی برای جلوگیری یا کاهش احتمال ترک سرد ناشی از هیدروژن مورد توجه است.
الف- استفاده از مواد مصرفی و فرآیندهای جوشکاری با هیدروژن کم، در جوشکاری با الکترود دستی مصرف الکترودهای قلیایی و پیش گرم کردن الکترود می تواند تا حدودی به کاهش هیدروژن در فلز جوش منجر شود. اما فرآیندهای دیگر جوشکاری نسبت به شرایط و امکانات ممکن است مقدار هیدروژن را به مینیمم برساند.و بعنوان مثال فرآیند جوشکاری با اشعه الکترونی
ب-امکان دادن برای رها شدن گاز از درون فلز گاه با عملیات پس گرم کردن کنترل درجه حرارت بین پاسها می توان به مقدار زیادی به هیدروژن این شانس را داد به بیرون نفوذ کند در بعضی فرآیندها ایجاد خلا در ضمن جوشکاری لازم می باشد خلا تقلیل فشار خارجی خروج گازها از جمله هیدروژن را تسهیل کرده و مقدار آنرا کاهش می دهد.
ج-کنترل ساختار میکروسکوپی میزان کربن و تنش های داخلی یا اعمال شده.
پس بطور کلی می توان گفت ترکهای گرم ، ترکهایی میباشند که در دماهای بالا رخ میدهند و معمولا به انجماد ربط دارند.ترکهای سرد ترکهایی هستند که بعد از اینکه جوش به دمای اطاق رسید، رخ دهد و ممکن است حتی به HAZ رابطه داشته باشد. بیشتر ترکها در اثر تنشهای فیزیکی انقباض که معمولا با کشیدن یا تغییر شکل جسم همراهی باشد در هنگام سرد شدن جوش رخ میدهد، ایجاد میشوند، اگر انقباض محدود شود، این تنشهای فیزیکی کرنشی ، تنش داخلی پسماند را بوجود میآورند که این تنشهای پسماند منجر به ایجاد ترک میشوند. در واقع دو نیروی مخالف وجود دارد:
1) تنشی که بوسیله انقباض ایجاد میشود.
2) استحکام و سختی فلز پایه
تنشهای ناشی از انقباض با افزایش حجم فلزی که تحت انقباض قرار گرفته است، افزایش مییابد. جوشهایی در ابعاد بزرگ و فرآیندهایی با نفوذ زیاد کرنشهای انقباضی را افزایش میدهند. تنشهایی که در اثر کرنشهای انقباضی ایجاد میشود با افزایش استحکام فلز پر کننده و فلز پایه افزایش مییابد. همچنین وقتی که استحکام تسلیم افزایش باید تنش پسماند نیز افزایش می یابد.
1) ضرورت جوشکاری
2) پیشگرم
3) دمای بین پالسی
4) عملیات حرارتی پس از جوش
5) طراحی اتصال
6) روشهای جوشکاری
7) مواد پر کننده
ترک به صورت خط مرکزی
ترک به صورت خط مرکزی در مرکز یک پاس جوش معین قرار دارد. در مورد پاس های چند تایی که چندین پاس در هر لایه وجود دارد ترک مرکزی از نظر هندسی ممکن است در مرکز اتصال قرار نداشته باشد. اگر چه اغلب دیده می شود که در مرکزاتصال قرار دارد. علت ترک مرکزی یکی از سه پدیده زیر می باشد:
1) ترکی که ناشی از جدایش و تفکیک باشد.
2) ترکی که مربوط به شکل گرده جوش میباشد.
3) ترکی که مربوط به تغییرات سطحی میباشد.
متأسفانه تمام سه پدیده فوق خودشان را در قالب یک نوع آشکار میکنند و تشخیص دادن ترک مشکل میباشد. علاوه بر این ، تجربهها نشان دادهاند که اغلب 2 یا حتی 3 پدیده فوق با یکدیگر برهمکنش داده و در ایجاد ترک مؤثرند. در واقع درک مکانیسم اصلی هر یک از انواع ترکهای مرکزی به ما کمک میکنند تا به دنبال راه حلی برای از بین بردن ترک باشیم.
ترک مرکزی ناشی از جدایش
این ترکها وقتی رخ میدهد که ترکیباتی با نقطه ذوب پایین نظیر فسفر ، روی ، مس و گوگرد در نقاط خاصی در حین فرآیند سرد شدن جدایش یابند. در حین فرآیند انجماد ، ترکیباتی با نقطه ذوب پایین در فلز مذاب به نواحی مرکزی اتصال رانده میشود چون آنها آخرین ترکیباتی هستند که شروع به انجماد میکنند و جوش در این نواحی تمایل به تفکیک و جدایش مییابد. در جوشکاری میتوان از الکترودهایی با مقادیر بالای منگنز استفاده تا بتوانیم بر تشکیل سولفید آهن با نقطه ذوب پایین غلبه کنیم. متأسفانه این مفهوم نمیتواند برای مواد غیر فرار دیگری بجز گوگرد بکار رود.
ترک مرکزی ناشی از شکل گرده جوش
نوع دوم ترک مرکزی ، ترک ایجاد شده در اثر شکل پاس جوش میباشد، این ترک در فرآیندهایی که همراه با نفوذ عمیق میباشند نظیر فرآیند FCAW , SAWتحت محافظ CO2 دیده میشود. وقتی که یک پاس جوشکاری دارای عمق بیشتری نسبت به هضم آن جوش (در نمای سطح مقطع) باشد. برای رفع این نوع ترک ، پاسهای جوش باید دارای عرضی حداقل برابر با عمق باشد. توصیه میشود که نسبت پهنای جوش به عمق آن برابر با 1 به 14/1 به 1 باشد تا این نوع ترک رفع شود. اگر از پاسهای چندتایی استفاده شود هر پاس دارای پهنای نسبت به عمق آن باشد، یک جوش فاقد ترک خواهیم داشت. وقتی که یک ترک مرکزی بخار شکل پاس تحت بررسی است، تنها راه حل این است که نسبت پهنای جوش به عمق آنرا تغییر دهیم.
این موضوع شاید در برگیرنده آن باشد که تغییری در طراحی اتصالها داشته باشیم. از آنجایی که عمق جوش تابعی از نفوذ میباشد شاید مفید باشد که مقدار نفوذ را کاهش دهیم بدین منظور میتوانیم از آمپرهای پایینتر و الکترودهایی با قطرهای بالاتر استفاده کنیم. راهکارهای فوق دانسیته جریان را کاهش میدهد و مقدار نفوذ را محدود میکند.
ترک مرکزی ناشی از شرایط سطحی جوش
آخرین مکانیسمی که سبب ایجاد ترک مرکزی میباشد تغییر شرایط سطحی میباشد. وقتی جوشهایی با سطح مقعر ایجاد میشود تنشهای ناشی از انقباضهای داخلی موجب میشود که سطح جوش کشیده شود. برعکس وقتی که سطح جوش محدب باشد نیروی ناشی از انقباضهای درونی موجب میشود که سطح جوش فشرده میشود. سطح جوش مقعر ، اغلب ناشی از ولتاژهای بالای قوس میباشد. کمی کاهش در ولتاژ قوس موجب میشود که گرده جوش به حالت محدب تغییر شکل دهد و تمایل به ترک حذف گردد. سرعتهای حرکت بالا نیز ممکن است به این موضوع کمک کند و کاهش در سرعت حرکت جوشکاری ، مقدار پراکندگی توسط جوش را افزایش میدهد و سطح جوش به صورت محدب تغییر حالت میدهد. جوشکاری در حالت قائم سر پایین باعث ایجاد این نوع ترک میشود. جوشکاری در حالت قائم رو به بالا میتواند از بروز این نوع ترک جلوگیری نماید.
ترک منطقه متأثر از جوش
ترک منطقه متاثر از جوش (HAZ) بوسیله جدایشی که بلافاصله مجاور گرده جوش رخ میدهد مشخص میشود، اگر چه این نوع ترک مربوط به فرآیند جوشکاری میباشد با این حال ترکی است که در روی پایه رخ میدهد نه درخود جوش. این ترک به نام تک مجاور جوش ، ترک گوشهای یا ترک تأخیری نیز نامیده میشود. چون این ترک بعد از اینکه فولاد در دمای f ْ400 انجماد یافته است رخ میدهد ترک انجمادی نیز نامیده میشود و چون با هیدروژن نیز همراه میباشد ترک همراه با هیدروژن نیز نامیده میشود. برای اینکه ترک HAZ رخ دهد سه شرط باید بطور همزمان برقرار باشد:
1) باید مقدار کافی هیدروژن وجود داشته باشد.
2) جوش باید به حد کافی نفوذ پذیر باشد.
3) باید به حد کافی تنشهای داخلی یا پسماند وجود داشته باشد.
حذف یکی از سه شرط فوق معمولا باعث میشود که این نوع ترک از بین برود. در جوشکاری ، یک راه برای حذف این نوع ترک این است که دو یا سه متغیر (مقدار جوش نفوذ پذیر جوش) را محدود کنیم. هیدروژن از منابع مختلفی میتواند وارد جوش شد. رطوبت و ترکیبات آلی منابع اصلی هیدروژن در جوش میباشند. هیدروژن میتواند در فولاد ، الکترود ، ترکییبات روپوش الکترود و در آتمسفر وجود داشته باشد.
ترک عرضی
ترک عرضی ترک متقاطع نیز نامیده میشود. ترکی است که در جهت عمود بر طول جوش ایجاد میشود. این نوع ترک از انواعی است که اغلب در جوشکاری با آن مواجه میشویم و معمولا جوشی که دارای استحکام بالاتری در مقایسه با فلز پایه میباشد دیده میشود. این نوع ترک میتواند همراه با هیدروژن نیز باشد و کل ترک منطقه متأثر از جوش HAZ که پیشتر شرح داده شد ناشی از مقدار بالای هیدروژن ، تنشهای پسماند و ریز ساختارهای حساس میباشد. فرق عمده بین این دو ترک این میباشد که ترک عرضی در فلز جوش نتیجه تنش پسماند طولی میباشد. چنانچه پاس جوشکاری بصورت طولی انقباض یابد، فلز پایه در مقابل این نیرو مقاومت میکند و در واقع دچار تراکم و فشردگی میشود. استحکام بالای فلز پایهای که در مجاورت جوش میباشد در برابر فشردگی ناشی از انقباض جوش مقاومت میکند و در واقع فشرده شدن جوش را محدود میکند. بخاطر ممانعتی که فلز پایه به عمل میآورد، تنشهای طولی در جوش گسترش مییابد.
وقتی با ترکهای عرضی مواجه میشویم باید سطح هیدروژن و شرایط نگهداری الکترودها را مد نظر داشته باشیم. در مورد ترک عرضی ، کاهش استحکام فلز جوش معمولا یکی از راهکارهای حذف این نوع ترک میباشد. تأکید زیادی بر روی فلز جوش وجود دارد چون فلز پر کننده به تنهایی ممکن است جوشی رسوب دهد که دارای استحکام پایینتری باشد و نیز تحت شرایط عادی فلزی نرم باشد. البته با تأثیر عناصر آلیاژی استحکام جوش بالا میرود و از نرمی آن کاسته میشود. استفاده از جوشهایی با استحکام پایینتر ، یک راه حل مؤثر در کاهش ترک عرضی مؤثر میباشد، البته به شریطی که استحکام جوش با استانداردهای تعریف شده مطابقت داشته باشد.
پیچیدگی
پیچیدگی یا اعوجاج تا حدی در تمام انواع جوشکاری وجود دارد، در بسیاری موارد آنقدر کوچک است که به سختی قابل رؤیت است، ولی در بعضی موارد باید پیش از جوشکاری به اعوجاجی که متعاقبا ایجاد میشود توجه کرد. مطالعه و بررسی اعوجاج بسیار پیچیده است و آنچه در ادامه آمده خلاصه است:
عوامل بوجیود آمدن اعوجاج :
1- حرارت دادن
2- عدم استفاده از وسایل مورد نیاز برای مهار کردن قطعه.
3- تنشهای پسماند موجود در قطعه
4- مناسب نبودن خواص قطعه کار
علل اعوجاج هنگامی که فلز تحت بار ، کرنش میکند یا حرکت میکند و تغییر شکل میدهد: تحت بار گذاری ضعیف فلزات بصورت الاستیک باقی میمانند. (به شکل اصلی خود باز میگردند یا پس از اینکه بار برداشته شد شکل میگیرند) که این تحت عنوان محدوده الاستیک شناخته میشود. تحت بار خیلی زیاد ، فلزات تا حدی تحت تنش قرار میگیرند که دیگر به شکل اول خود باز نمیگردند یا شکل نمیگیرند و این نقطه (نقطه تسلیم) نامیده میشود (تنش تسلیم)
فلزات با حرارت دیدن انبساط مییابند و وقتی سرد میشوند منقبض میشوند، فلزات در حین جوشکاری گرم و سرد میشوند که موجب تنشهای بالای ناگهانی و اعوجاج میشوند. اگر این تنشهای زیاد از محدوده الاستیک بگذرند و از نقطه تسلیم نیز رد شوند، برخی پیچیدگیهای دائمی در فلز پدید میآید، تنش فلز در دمای بالا کاهش مییابد. اعوجاج اثر ناخواسته انبساط و انقباض فلز حرارت دیده است.
انواع پیچیدگی
سه نوع اصلی پیچیدگی وجود دارد:
1) زاویهای

2) طولی
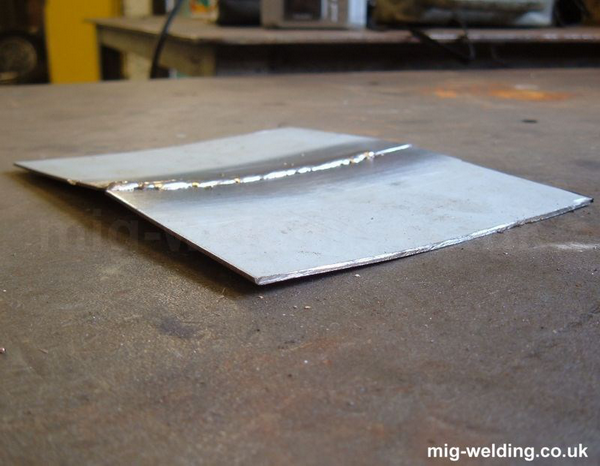
3) عرضی
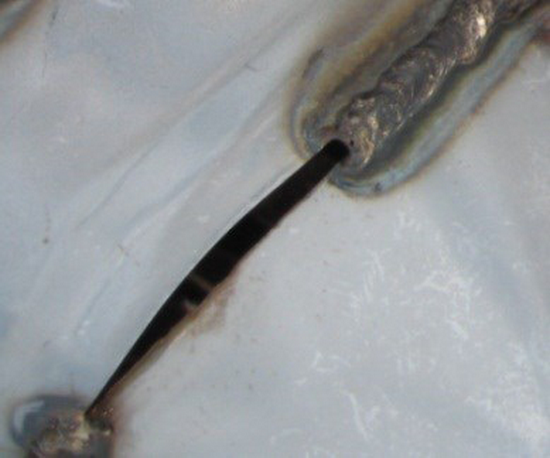
کنترل پیچیدگی میتواند در سه مرحله انجام گیرد:
• قبل از جوشکاری
• حین جوشکاری
• بعد از جوشکاری
کنترل پیچیدگی قبل از جوشکاری توسط روشهای زیر انجام میشود:
1) خال جوش زدن
2) گیره ، بست و نگهدارنده
3) پیشگرم کامل و سرتاسری
4) مونتاژ اولیه مناسب
کنترل اعوجاج پس از جوشکاری:
1) سرد کردن آرام
2) صافکاری شعلهای (حرارت دهی معکوس)
3) آنیل کردن
4) تنش زدایی
5) نرمال کردن
6) صافکاری مکانیکی
در سازههای فلزی ساختمان معمولا روشهای 1و2 بیشتر اعمال میگردد و سایر روشها در کارهای صنعتی بیشتر کاربرد دارند.
آنیل کردن
یک پروسه عملیات حرارت است که برای نرم کردن فلزات جهت کار سرد یا ماشین کاری بکار میرود، قطعه یا کار نهائی معمولا در کوره تا دمای بحرانی (برای فولاد با 52/0 % کربن حدود Cْ 820- 723 ) حرارت داده میشود و سپس به آرامی سرد میشود.
تنش زدائی
حرارت دهی یکنواخت قطعات جوش شده تا دمایی زیر دمای بحرانی است که با سرد کردن آرام دنبال میشود، این پروسه نقطه تسلیم فلز را کاهش میدهد، لذا تنشهای باقی مانده در قطعه کاهش مییابد.
نرمال کردن
پروسهای برای ریز کردن ساختار دانهای فلز است که موجب بهبود مقاومت آن در برابر شوک و خستگی میشود. در نرمال کردن قطعات جوش شده تا بالای دمای بحرانی Cْ 820 برای فولاد با کربن 0.25% (تقریبا یک ساعت برای هر nm 25 ضخامت حرارت میبیند و سپس در هوا سرد میشود) (مستقیم کاری).
چاله سیاه (Black point) – چاله انتهایی جوش
عیبی در جوشکاری وجود دارد که در انتهای جوش در آخرین حوضچه بوجود می آید و بصورت سوراخی در انتهای جوش به وجود میآید. علت این عیب آن است که وقتی جوشکار در انتهای جوشکاری انبر را به بالا می آورد الکترونهایی که از الکترود به سمت حوضچه جوش حرکت می کنند در هنگام بالا بردن الکترود تا فاصله مشخص این حرکت توسط الکترون ها ادامه دارد و با برخورد به سطح قطعه سوراخی پدید می آید ولی به علت طول قوس بالا این قسمت پوشش نمی شود و در نتیجه این سوراخ توخالی باقی می ماند.
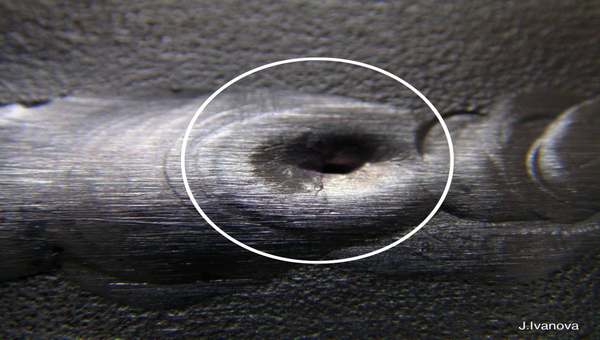
راه پیشگیری از این عیب
برای اینکه این عیب در جوش به وجود نیاید جوشکار باید هنگامی که به پایان جوشکاری می رسد مقداری به عقب بر می گردد و در هنگامی که می خواهد انبر در را از روی حوضچه جوش بردارد باید زاویه انبررا با قطعه بسیار کم کند تا حرکت الکترونها از الکترود به سمت حوضچه جوش که به صورت عمودی است از بین برود و در نتیجه این عیب بوجود نیاید.
ترشح یا جرقه Spatter
قطرات ریز فلز را که از منطقه جوش اثنای اتصالات ذوبی به اطراف پرتاب می شوند جرقه یا ترشح می گویند. این قطرات ممکن است از حوضچه جوش یا بیشتر از الکترود و مفتول پرکننده ناشی شده باشد. هنگامی که دانه های کروی و بزرگ از قطرات مذاب از الکترود به طرف حوضچه جوش منتقل می شود و ایجاد پل در فاصله قوس می کند. مداری بسته Short circuit بوجود می آید که عبور شدت جریان از آن باعث گداخته شدن فوق العاده این پل می گردد که با انفجار آن بارانی از جرقه های گداخته به اطراف حاصل می شود.
وقوع جرقه بوسیله تعدادی واکنش در فرآیندهای گوناگون افزایش می یابد. مقدار گاز اضافی ایجاد شده در اثر سریع سرد شدن مذاب واکنش بین عناصر معین در فلز مذاب به عنوان مثال گوگرد با بعضی گازهای اتمسفر در منطقه حوضچه جوش، نمونه هایی از این نوع واکنش های جرقه زا می باشند. جرقه های درشت در فرآیند جوشکاری با الکترود دستی در اثر طول قوس اضافی و جرقه های ریز ناشی از شدت جریان اضافی ایجاد می شود.
جرقه ها اغلب در حین پرواز در اتمسفر اکسید شده و بر روی سطح فقط ایجاد لکه هایی می کنند. اغلب جرقه های چسبیده شده بر روی سطح در فواصل دور آسان تر با برس سیمی یا وسایل مشابه تمیز می شوند اما جرقه های چسبیده شده در نزدیکی مسیر اتصال براحتی تمیز نمی شوندو ظاهر جوش را بد منظر می کند. از طرف دیگر لکه های باقیمانده بر روی سطح می توانند شبیه لکه های قوس موجب عوارضی شوند. علاوه بر نکات بالا جرقه و ترشح یکی از مشکلاتی است که غالبا جوشکارها را با سوزاندن پوست و یا لباس آزرده و ناراحت می کند و حتی الامکان باید از ایجاد آن جلوگیری کرد. غالبا با تنظیم پارامترهای جوشکرای (آمپر، قطب و ولتاژ) یا تعویض الکترود می توان این مشکل را کاهش داد.
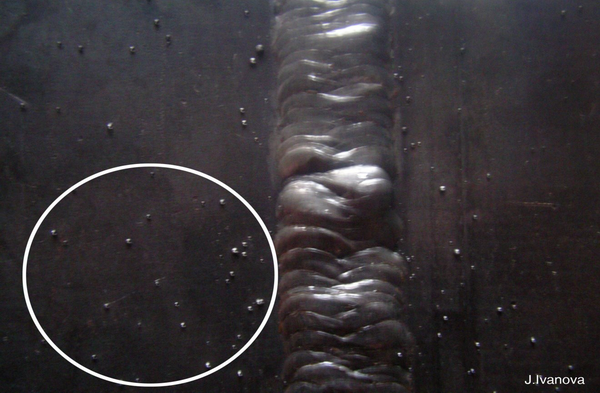
عوامل ایجاد پاشش :
1.طول قوس بلند: هنگامی که فاصله الکترود با قطعه کار زیاد باشد ذرات مذابی که از سمت الکترود به طرف فلز می آیند. دمایی در حدود (دمای فلز تقریبا 1500 درجه سانتیگراد)، باید دمای قوس که حدود 5000 درجه سانتیگراد می باشد را متحمل شوند، وقتی طول قوس زیاد باشد قطره مذاب باید در مسافت بیشتر دمای قوس را متحمل شود ولی نمی تواند در مسیر منفجر می شود و به روی قطعه پاشیده می شود که در نتیجه این عیب به وجود می آید.
2.شدت جریان زیاد: هنگامی که شدت جریان زیاد باشد دمای طول قوس افزایش می یابد (حدود 5000 درجه سانتیگراد) و در نتیجه قطرات مذاب نمی توانند این دما را تحمل کنند و منفجر می شوند و به روی قطعه پاشیده می شوند.
3.پوشش آسیب دیده: هنگامی که روپوش الکترود ما آسیب دیده باشد الکترود به طور کامل نمی تواند عمل پوشش از منطقه مذاب را انجام دهد و به همین خاطر در همان قسمتی که الکترود کار پوشش را به درستی انجام نمی دهد قوس تعادل خود را از دست می دهد و باعث پاشش مذاب به قسمتهای مختلف قطعه می شود.
4.انحراف قوس: در زمانی که قوس دچار انحراف می شود تعادل در جوشکاری از بین می رود و قوس ناپایدار می شود و به همین دلیل باعث می شود پاشش مذاب بیشتر شود.
لکه قوس Arc stricks
معمولا جوشکارهای بی دقت برای شروع قوس با الکترود دستی ابتدا الکترود را بر روی سطح کار در یک یا چند نقطه به طور لحظه ای میمالند تا بدین ترتیب قوس های موقتی ایجاد شده و با گرم شدن نوک الکترود روشن کردن قوس در محل شروع عملیات جوشکاری تسهیل یابد. نقاط تماس لحظه ای الکترود با سطح کار بصورت لکه هایی مشاهده می شود که در حقیقت لایه نازکی از سطح کار می باشد که در اثر ایجاد قوس موقت ذوب و سپس سریع سرد شده است. سطح مقطع این لکه ها در زیر میکروسکوپ ساختار مارتنزیتی بسیار ترد و شکننده ای را نشان می دهد که اغلب دارای ترکهای ریزی نیز می باشد. علاوه بر این چون زمان قوس موقت بسیار کوتاه است فرصت ذوب پوشش الکترود و ایجاد لایه محافظ سرباره یا گاز نمی باشد در نتیجه این لایه نازک ذوب شده در سطح کار در تماس با اکسیژن و ازت از اتمسفر قرار می گیرد و عدم ورود بعضی ترکیبات آلیاژی یا اکسیژن زدا از پوشش الکترود به منطقه خلل و فرج و ذرات اکسیدی زیادی در این لایه بوجود می آید. این عوامل سبب می شود که اگر احیانا قطعه کار به طریقی تحت تنش قرار گیرد که لکه های نامبرده در مواضع حساس قرار گیرند می توانند حتی در فواصل دور از محل اتصال نیز نقاط تمرکز تنش شده و منجر به ترک برداشتن یا گسیختگی قطه کار شوند.
بنابراین جوشکار باید توجه کند که تا اولا تماسهای لحظه ای لازم برای شروع قوس ابتدایی را در هر الکترود بر روی قطعه ای قراضه که در مجاور اتصال قرار داده انجام دهد ثانیا اگر غفلتا بر روی کار این عمل انجام گرفت آنرا با سنگ زدن تمیز کرده و یا با جوش کامل و سالم روی آنرا بپوشاند، ثالثا سعی کند این لکه قوس ها را در مسیر مورد اتصال ایجاد کند تا بعد از رسیدن قوس بر روی آن این آثار محو شود.
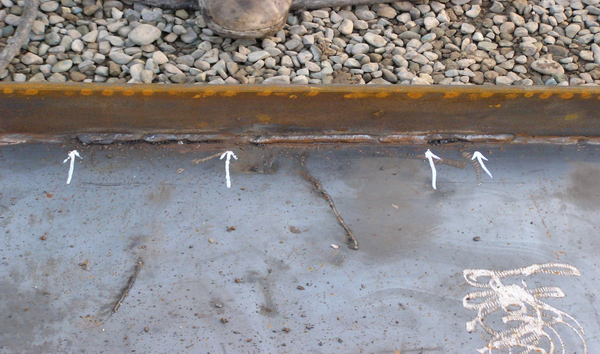
تقعر در گرده جوش (Concavity)
دلایلی که باعث به وجود آمدن این عیب می شود
1) سرعت زیاد : هنگامی که سرعت جوشکاری بالا باشد کانالی توسط برخورد الکترونها از الکترود به قطعه به وجود می آید و از طرف دیگر مواد مذابی که وظیفه پر کردن این کانال را دارند برای اینکه سریعتر این کار را انجام دهند نمی توانند به طور کامل کارشان را انجام دهند در نتیجه کانال به طور کامل و به اندازه کافی پر نمی شود و این عیب به وجود می آید.
2) شدت جریان بالا : هنگامی که شدت جریان در جوشکاری زیاد باشد، پاشش مذاب هم افزایش می افتد همچنین نفوذ در جوشکاری بیشتر می شود در نتیجه بنابراین دو اصل وقتی شدت جریان افزایش می یابد از طرفی کانالی که توسط الکترونها حفرمی شود عمق بالایی دارد و از طرف دیگر ذرات مذابی که وظیفه پر کردن این کانال را دارند به دلیل پاشش زیاد مقدارشان کمتر می شود و وقتی در این کانال رسوب می کنند نمی توانند بطور کامل این کانال را پر کنند و این عیب به وجود می آید.
تحدت در گرده جوش (Convexity)
دلایل به وجود آمدن این عیب دقیقا برعکس تقعر در جوشکاری می باشد.
1) سرعت جوشکاری کم باشد
2) شدت جریان در جوشکاری پایین باشد
پس گرمی و پیش گرمی
در جوشکاری فولادهای پرکربن با آلیاژی همیشه خطری وجود دارد که فلز جوش نشسته (weld deposit) و ناحیه متاثر از جوش (heat-affected zone) فلز سخت و شکننده ای بنام مارتنزیت (martensite) تشکیل دهند. در اینصورت فلز نرمی (ductility) خود را از دست داده و امکان ترک خوردن هنگام سرد شدن دارد. با استفاده از پیش گرمی و پس گرمی می توان میزان مارتنزیت جوش را در حداقل نگهداشت.
پیش گرمی و پس گرمی دمای فلز مجاور جوش را بالا برده و در نتیجه اختلاف دمای بین جوش و فلز مجاورآنرا تا حد امکان پایین نگه می دارد. فولادهای کم کربن به ندرت نیاز به پیش گرمی دارند. از آنجایی که سختی پذیری فولاد نسبت مستقیم با میزان کربن و عناصر آلیاژی دارد دماهای پیش گرمی مختلف خواهد بود. کربن معادل (%) تا 45/0 پیش گرمی اختیاری می باشد کربن معادل (%)45/0 تا 60/0 دمای پیش گرمی200تا400 درجه فارنهایت کربن معادل (%) بالای 60/0دمای پیش گرمی 400تا 700 درجه فارنهایت می باشد.
پس گرمی: هدف از پس گرمی مشابه پیش گرمی می باشد در حقیقت پس گرمی همراه با پیش گرمی استفاده می شود بوسیله حرارت دادن قطعه جوش خورده همینکه جوش تکمیل شد دما قطعه کار را می توان در دمای بالایی نگه داشت تا جوش به آرامی سرد شود. همچون پیش گرمی هر گونه عملیات پس گرمی ناحیه جوش خورده را نرم تر نگه می دارد. دماهای پس گرمی و مدت زمان آن به نوع و ضخامت فولاد بستگی دارد. دما از 600 درجه فارنهایت برای فولاد نوع 10xx تا 1200 درجه فارنهایت برای فولادهای 43xx می تواند تغییر کند این در حالی است که زمان مورد نیاز جهت پس گرمی از 5 دقیقه تا چندین ساعت متغیر می باشد.
تاثیر عناصر در فولاد
عناصر مختلف که بطور متداول در فلزات یافت می شوند تاثیر مشخصی روی قابلیت جوشکاری آنها دارند بعضی از این عناصر مهم و اثرات حاصل از آنها بر جوشکاری فولاد عبارتند از:
1.کربن (Carbon) : از آنجایی که میزان سختی پذیری (hardenability) در فولاد را معین می کند مهمترین عنصر موجود در فولاد است. هر چه میزان کربن بیشتر باشد فولاد سخت تر می شود. اگر فولاد کربنی (بالای 30/0 درصد) جوشکاری شود و ناگهان سرد شود یک ناحیه ترد و شکننده (brittle) در کنار جوش ایجاد می گردد بعلاوه اگر کربن اضافی از مخلوط گازهای جوشکاری بدست آید جوش بوجود آمده آنقدر سخت می شود که به آسانی ترک می خورد. بطور کلی بهترین جوش هنگامی ایجاد می شود که میزان کربن موجود در فولاد تا جای ممکن کمترین حد خود باشد.
2.منگنز (Manganese) : در فولاد باعث افزایش سختی پذیری و استحکام کششی (tensile strength) می شود به هر حال اگر مقدار منگنز بالای 60/0 درصد باشد و بخصوص اگر با درجه بالایی از کربن ترکیب شود قابلیت جوشکاری قطعا کم خواهد شد. در این شرایط معمولا ترک افزون ایجاد خواهد شد.و اگر میزان منگنز خیلی کم باشد تخلخل داخلی (internal porosity) و ترک ممکن است گسترش یابد. بهترین نتیجه جوشکاری وقتی بدست می آید که فولاد محتوی 40/0 تا 60/0 درصد منگنز باشد.
3.سیلیکون (Silicon) : برای بهبود کیفیت و استحکام کششی در فولاد بکار می آید میزان بالای سیلیکون بخصوص همراه با کربن بالا منتج به ترک می شود.
4.گوگرد (Sulfur) : اغلب برای بهبود خواص ماشین کاری (machining) فولاد به آن اضافه می گردد. به هر حال مقدار آن در انواع دیگر فولاد پایین نگه داشته می شود (035/0 درصد و حداکثر 05/0 درصد) زیرا که در صد بالای گوگرد احتمال ترک را افزایش می دهد. فولادهای ماشینی پرگوگرد بطور معمول با الکترود کم هیدروژن بدون هیچ دشواری جوشکاری می شوند.
5.فسفر (Phosphorus) : به عنوان ناخالصی در فولاد در نظر گرفته می شود در نتیجه مقدار آن تا حد امکان پایین نهداشته می شود میزان فسفر بالای 04/0 درصد باعث می شود که جوش شکننده (brittle) شود.
6.عناصر دیگر (نیکل، کروم، وانادیم و غیره)تاثیرهای مختلفی بر قفابلیت جوشکاری فلزات دارند. جوشکاری این آلیاژها باید با احتیاط خاصی انجام گیرد و معمولا برای جلوگیری ایجاد نواحی سخت و شکننده در جوش پیش گرمی (preheat) و پس گرمی (postheat) مورد نیاز می باشد.